Lean Six Sigma Foundations - Yellow Belt
Lean Six Sigma Foundations - Yellow Belt
Skills you’ll gain
Lean Six Sigma is a proven business process improvement methodology for companies striving to gain a competitive edge. In high demand across a diverse range of industries, Lean Six Sigma training is a powerful way to become an indispensable asset at your organization and improve your career prospects.
In this online course, you will gain a solid foundation in the methodology, principles, and tools needed to be a valuable member of a Lean Six Sigma team. In addition, this course is designed to prepare you for the International Association of Six Sigma Certification (IASSC) Yellow Belt exam.
Course highlights:
- 42 practical video tutorials with reference guides, exercises, and quizzes.
- Earn 17 PDUs or contact hours toward your Project Management education for certification with PMI.
- Expert instruction by a certified Project Management Professional (PMP) with the Project Management Institute, a certified Scrum Master with Scrum Alliance, and certified Lean Six Sigma Black Belt with IASSC. Ray Sheen is a member of the Project Management Institute and the Product Development Management Association.
- Aligned to the IASSC Lean Six Sigma Black Belt Body of Knowledge.
This course covers:
- The requirements and application process for Lean Six Sigma certification with internationally recognized accreditation body, IASSC. Lean Six Sigma principles and how the Lean and Six Sigma methodologies complement each other.
- The roles, phases, and deliverables of a Lean Six Sigma project.
- Lean Six Sigma fundamentals including Critical to Quality (CTQ), variation, and process management.
- Essential materials to build competency in the Define, Measure, and Control phases.
- Knowledge of Basic Six Sigma statistics, including normal distribution, basic graphical analysis, and process stability.
The only method to earn an IASSC certification is to successfully sit for and pass an official IASSC certification™ exam, which can be taken through IASSC. We do not provide access to IASSC Certification exams.
Looking for something else? We offer a range of project management and Lean Six Sigma online training, including Black Belt and Green Belt certification courses.
Once enrolled, our friendly support team and tutors are here to help with any course-related inquiries.
Syllabus
Download syllabus-
1
IASSC Testing Approach The International Association of Six Sigma Certification is a recognized international body that certifies Lean Six Sigma Yellow, Green, and Black Belts. The online application process is straightforward. 5m
-
2
IASSC Yellow Belt The IASSC Yellow Belt certification focuses on the Define, Measure, and Control phases of a Lean Six Sigma Project. 5m
-
1
Roles and Responsibilities The Lean Six Sigma methodology has defined roles of Yellow Belt, Green Belt, Black Belt, and Master Black Belt with respect to project leadership and execution. In addition, there are roles and responsibilities for team sponsors, team members, and others who become involved with a Lean Six Sigma project. 4m
-
2
Project Charter A best practice for any project is to create a project charter at the time of project initiation. The Lean Six Sigma project charter will focus on the scope of the project, the timing for the project milestones, and the key team members. This provides a basis for project planning. 4m
-
3
Project Phases The Lean Six Sigma methodology relies on a five-phased project management methodology. The phases Define, Measure, Analyze, Improve, and Control provide structure to the project. 5m
-
4
Project Deliverables The Lean Six Sigma methodology has defined a set of deliverables that should be prepared during each of the five project phases. These deliverables will guide a project team through the improvement process in an orderly and logical manner. 5m
-
1
Critical To Quality (CTQ) Lean Six Sigma relies on the use of Critical to Quality (CTQ) characteristics. These are the attributes that will be used to measure success or failure of the project. 4m
-
2
Y=F(x) Lean Six Sigma projects strive to characterize project performance through the creation of a process formula. This formula allows the team to determine controllable factors and predict and optimize process performance. 4m
-
3
Process Management Lean Six Sigma analysis considers process level performance. For this reason it is necessary to understand the complete process – both the process steps and the process flow. 5m
-
4
Project Metrics Lean Six Sigma has introduced some new metrics into the common business vocabulary including process sigma, DPMO, cycle time, and value-added effort. 8m
-
5
Variation Variation leads to uncertainty in process performance which requires extra management and buffers elsewhere in the business environment. One of the primary goals of a Lean Six Sigma project is to identify sources of variation in process performance and eliminating or reducing those sources of variation. 6m
-
6
Elements of Waste Waste can take many forms including high costs, delayed timing, rework, redundant work and idle processes. One of the primary goals of a Lean Six Sigma project is to identify areas of process waste and eliminating or reducing those sources of waste. 6m
-
1
Project Selection One of the decisions that must be made during the Define Phase is the selection of the project and its boundaries. Lean Six Sigma projects are often part of a portfolio of projects that may be selected and approved as a bundle. 5m
-
2
Voice of the Customer Lean Six Sigma methodology is grounded on the voice of the customer. The Define phase collects and assesses information concerning the customer perspective and uses it to focus the project activities. 6m
-
3
Cost of Poor Quality (COPQ) Lean Six Sigma is a problem-solving methodology. As such, one of the ways of quantifying the opportunity for improvement is through an aggregation of the costs associated with that problem. This is known as the Cost of Poor Quality and provides insight into the project benefit. 7m
-
4
Process Mapping In order to improve process performance, the Lean Six Sigma project team must understand the current state of the process. Process Mapping is the technique for describing the process and providing a framework for collecting process data. 5m
-
5
Pareto Principle The Pareto principle is a widely accepted technique for prioritizing effort and activity. The Pareto principle will typically be applied in every phase of a Lean Six Sigma project, including this initial Define phase where it is used to prioritize the areas of focus for the project. 4m
-
6
Lean Value Lean Six Sigma projects apply the Lean principle of value-added effort in the definition of the project and when identifying the opportunity for improvement. 5m
-
1
Data Types There are three types of data: variable, attribute and ranked. Each type is useful in measuring process performance by analyzing process problems, but they need to be treated differently. 5m
-
2
X/Y Matrix The X/Y Matrix is a tool that maps the Voice of Customer needs and concerns (Y) onto the process steps and inputs (X). This tool can take on several different formats, but any of them will provide the Lean Six Sigma team with insight into the contributing factors of customer value. 4m
-
3
Intro to FMEA The Failure Mode Effects Analysis (FMEA) tool highlights areas of high product design or process execution risk. This tool provides insight into possible causes for observed failures. 6m
-
4
Value Stream Mapping Value stream mapping is the Lean process mapping technique. With this map, the Lean Six Sigma team will know which steps are directly contributing to delivering the customer value aspects of the process. It also provides the foundation for deeper flow analysis. 4m
-
5
Problem Statement The problem statement clarifies the goals and activities of the Lean Six Sigma project by specifying the issue to be resolved. It's an excellent communication tool for the team to use with stakeholders. 4m
-
6
Problem Definition Tools There are numerous tools to assist the Lean Six Sigma team in the creation of the problem statement. Different tools work better in different applications, but all of them help the Lean Six Sigma team focus on the root cause problems and not chase symptoms. 6m
-
7
Measurement Systems The collection of data assumes that there is a measurement system used to measure and record the data. It is important to understand the characteristics of the measurement systems so that the Lean Six Sigma team will know how far they can trust the data. 5m
-
8
Measurement Errors All measurement systems introduce an element of error into the measured value. There are techniques for determining the magnitude of that error and thereby determining if a different measurement system needs to be used. 5m
-
1
Process Capability - Attribute Data A stable process is one in which only random variation exists. A Lean Six Sigma team must eliminate sources of instability before attempting to improve the normal process performance. To determine stability with attribute data, lookup tables and yield rates must be used. 4m
-
2
Normal Distribution The normal distribution charts the type of variability in a process parameter that is being measured when the only cause for variation is natural random physical effects. It's the desired distribution when improving a process since it delivers a predictable level of process performance. 6m
-
3
Process Stability A stable process is one in which only random variation exists. A Lean Six Sigma team must eliminate sources of instability before attempting to improve the normal process performance. The key is undertanding common cause and special cause variation.. 6m
-
4
Process Capability - Variable Data Process capability is the statistical analysis conducted to determine if a process performing with only the normal process variation can be expected to meet the customer's expectations at all times. Variable data process capability is tracked with capability indices. 7m
-
5
Descriptive Statistics Lean Six Sigma methodology relies heavily on statistical analysis of problems and solutions. A single data point is not sufficient, rather a collection of data is needed for analysis. This collection will have some natural variability within it and descriptive statistics explain the boundaries of that variability. 6m
-
6
Basic Graphical Analysis When considering a distribution of data values for a process attribute, a graph of that data can be very insightful. The picture is often easier for team members to understand than a statistical description of the data distribution. This picture will often point the team to the process problem. 4m
-
7
Run Chart The run chart is the most common chart of process data. It is easy to create and maintain and gives the process operators immediate insight when a process becomes unstable. 5m
-
1
Cost-Benefit Analysis The cost-benefit analysis quantifies the financial impact of the Lean Six Sigma project. It includes the project costs and the operational impacts which could include cost savings, new cost of new operations, and the gross margin impact of additional sales. 3m
-
2
Control Plan It is hard to make a permanent change to a process. People and systems have a tendency to drift back to the old way of doing things. The control plan provides guidance on how to maintain control of the new process and the measurements that will show the process deviating from the new approach. 4m
-
3
Response Plan A key element of the control plan is the response plan. It tells the process operators what to do when the process begins to deviate from the parameters laid out in the control plan. 7m
-
4
Prevention as Control One of the best techniques for controlling a process to perform in a particular manner is to prevent it from performing in any other manner. There are methodologies that can be used to create prevention of process problems: Poke Yoke and Five S Disciplines. 6m
Certificate
Certificate of Completion
Awarded upon successful completion of the course.

Instructor
Ray Sheen
Ray is a certified Project Management Professional (PMP) with the Project Management Institute, a certified Scrum Master with Scrum Alliance, and certified Lean Six Sigma Black Belt with IASSC. He is a member of the Project Management Institute and the Product Development Management Association.
He is president and founder of Product & Process Innovation, Inc. and is a veteran business leader with over 25 years of executive, project management, and engineering management experience. Ray has worked in several industries including aerospace, electrical distribution and utilities, biotechnology, appliances, electronics, machining, medical devices, pharmaceutical, automotive, and financial services. He has held executive management positions in a Fortune 500 company and has been involved in entrepreneurial startup organizations.
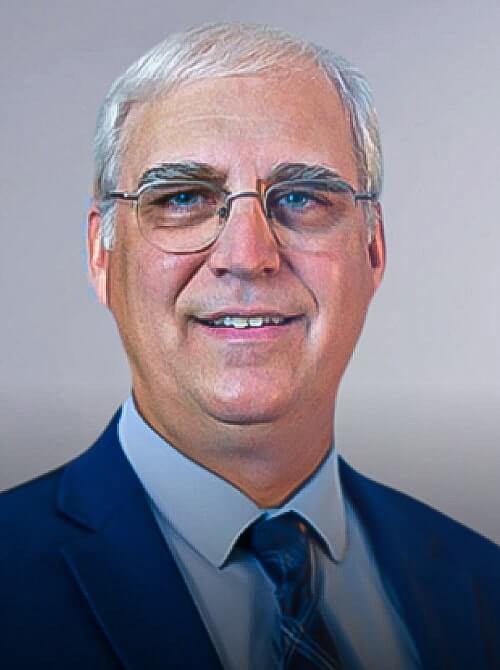
Ray Sheen
Project Management Instructor & Author
Accreditations
Link to awards The PMI ATP seal, PMI, PMP, CAPM and PMBOK are registered marks of the Project Management Institute, Inc.How GoSkills helped Chris
I got the promotion largely because of the skills I could develop, thanks to the GoSkills courses I took. I set aside at least 30 minutes daily to invest in myself and my professional growth. Seeing how much this has helped me become a more efficient employee is a big motivation.
