Online FMEA Training Course | Failure Mode and Effects Analysis
Failure Mode and Effects Analysis
Skills you’ll gain
This course is part of our Lean Six Sigma Black Belt program, which consists of eight courses designed to prepare you for the International Association of Six Sigma Certification (IASSC) Black Belt exam. We recommend you take all eight courses in the program to be fully prepared for the exam.
What you will learn
In this online FMEA training course, you will master Failure Mode Effects Analysis, or FMEA, a technical risk analysis tool that both assesses risks of a product or process failure and prioritizes those risks for mitigation.
The Design FMEA focuses on product risk and is best applied when doing that risk assessment during the development process. The Process FMEA is both helpful during the development of the process and with the ongoing management and improvement of the process. Both techniques rely on the participation of a cross-functional team and they provide an objective score to what is often a subjective discussion within an organization.
By the end of the course, you will have learned how to conduct a Failure Mode Effects Analysis. If you are a member or leader of an analysis team using a methodology such as Lean Six Sigma, this analysis will be a significant aid to your problem resolution.
Who this online FMEA training course is for
This course can be taken as part of the GoSkills Lean Six Sigma Black Belt training program, to prepare for certification with IASSC. It is also a good stand-alone course for anyone in an industry where FMEAs are part of normal product and process development.
This course will be from the standpoint of helping you to make wise decisions about your product and process design and management, not conducting mathematical proofs or solving partial differential equations. To assist you with your learning, I will provide templates of typical FMEA forms and spreadsheets.
Highlights:
- 28 practical tutorials with videos, reference guides, exercises and quizzes.
- Downloadable FMEA forms, templates, and spreadsheets.
- Designed to prepare you in part for the IASSC Black Belt exam. To prepare in full, you should take all eight courses in our Lean Six Sigma Black Belt program.
- Understand the various types of FMEAs used in different business processes.
- Master the Failure Mode and Effects methodology, including the process, standards, and types of failures.
- Learn how to conduct a Process FMEA, from preparation, analysis, mapping, failure modes and ratings.
- Learn how to conduct a Design FMEA, from preparation, analysis, mapping, failure modes and ratings.
- Gain critical skills for your role in the product and process development industry or Lean Six Sigma team.
- Earn 4.5 PDUs or contact hours toward your Project Management education for certification with PMI.
Once enrolled, our friendly support team and tutors are here to help with any course related inquiries.
Syllabus
Download syllabus-
1
FMEA Process FMEAs are completed using a seven step process. There are minor variations in the process based upon the type of FMEA. The results of the FMEA analysis are recorded on a standard FMEA form. 4m
-
2
FMEA Team The FMEA analysis is normally conducted by a cross-functional team. A team of subject matter experts is a critical element of FMEA success. 5m
-
3
FMEA Standards and Definitions The FMEA is a widely accepted methodology across many industries. There are several standards that provide guidance on how to determine the FMEA scoring for different types of FMEAs. 5m
-
4
Types of Failures There are many types of failures. When conducting an FMEA, all failure types must be considered, not just the most obvious. Each category of failure should be considered for every product component or process step. 8m
-
5
Failure Mode and Effects Criticality Analysis (FMECA) The FMECA is a special form of FMEA that accentuates the focus on finding and controlling critical characteristics. It simplifies the FMEA process, but loses fidelity in the analysis. 5m
-
6
Critical Characteristics Critical characteristics drive cost and complexity in process operations. Design FMEAs identify critical characteristics. Process FMEAs assess the ability of the organization to control critical characteristics. 5m
-
1
Design FMEA Preparation The first three steps of the Design FMEA process set the stage for effective FMEA analysis sessions. Cutting corners on these steps lead to confusion and delays in the analysis. 5m
-
2
Design FMEA Analysis The final four steps of the Design FMEA are where the assessment happens. These steps do the original analysis and manage the mitigation of high risk failures. 5m
-
3
DFMEA Block Diagram Failures are based upon the product or system's functional design The functional block diagram of the system or product initiates the FMEA analysis. 6m
-
4
DFMEA Failure Modes Each of the functions identified in the block diagram are susceptible to failures. These failures are identified and recorded on the FMEA. 5m
-
5
DFMEA Severity Rating An effect on the customer or user is determined for each failure mode and listed in the Design FMEA. The severity of that effect is rated to determine the impact. 6m
-
6
DFMEA Occurrence Rating Causes for each failure in the Design FMEA are identified. The probability of each of those causes occurring is evaluated and scored. 8m
-
7
DFMEA Detection Rating The product design and development process is evaluated to determine if it is able to detect each of the failures listed in the Design FMEA. This detection capability is evaluated and scored. 7m
-
8
DFMEA RPN and Mitigation The severity, occurrence, and detection ratings are combined to create a Risk Priority Number (RPN). When that RPN exceeds the organization's risk threshold for Design FMEAs, a mitigation strategy is developed and implemented to lower the scores until the RPN is acceptable. 7m
-
1
Process FMEA Preparation The first three steps of the Process FMEA process set the stage for effective FMEA analysis sessions. Cutting corners on these steps lead to confusion and delays in the analysis. 5m
-
2
Process FMEA Analysis The final four steps of the Process FMEA are where the assessment happens. These steps do the original analysis and manage the mitigation of high risk failures. 5m
-
3
Process Mapping Failures are based upon the process steps. A process map identifies all the steps in the process. These steps initiate the Process FMEA. 6m
-
4
PFMEA Failure Modes Each of the steps identified in the process map are susceptible to failures. These failures are identified and recorded on the FMEA. 6m
-
5
PFMEA Severity Rating An effect on process performance or operator safety is determined for each failure mode and listed in the Process FMEA. The severity of that effect is rated to determine the impact. 6m
-
6
PFMEA Occurrence Rating Causes for each failure in the Process FMEA are identified. The probability of each of those causes occurring is evaluated and scored. 6m
-
7
PFMEA Detection Rating The process is first assessed to determine if the failure modes identified in the Process FMEA have been prevented based upon the process design or management. The process control plan is then evaluated to determine if it is able to detect each of the failures listed in the Process FMEA. This prevention and detection capability is evaluated and scored. 6m
-
8
PFMEA RPN Rating and Mitigation The severity, occurrence, and detection ratings are combined to create a Risk Priority Number (RPN). When that RPN exceeds the organization's risk threshold for Process FMEAs, a mitigation strategy is developed and implemented to lower the scores until the RPN is acceptable. 7m
Certificate
Certificate of Completion
Awarded upon successful completion of the course.

Instructor
Ray Sheen
Ray is a certified Project Management Professional (PMP) with the Project Management Institute, a certified Scrum Master with Scrum Alliance, and certified Lean Six Sigma Black Belt with IASSC. He is a member of the Project Management Institute and the Product Development Management Association.
He is president and founder of Product & Process Innovation, Inc. and is a veteran business leader with over 25 years of executive, project management, and engineering management experience. Ray has worked in several industries including aerospace, electrical distribution and utilities, biotechnology, appliances, electronics, machining, medical devices, pharmaceutical, automotive, and financial services. He has held executive management positions in a Fortune 500 company and has been involved in entrepreneurial startup organizations.
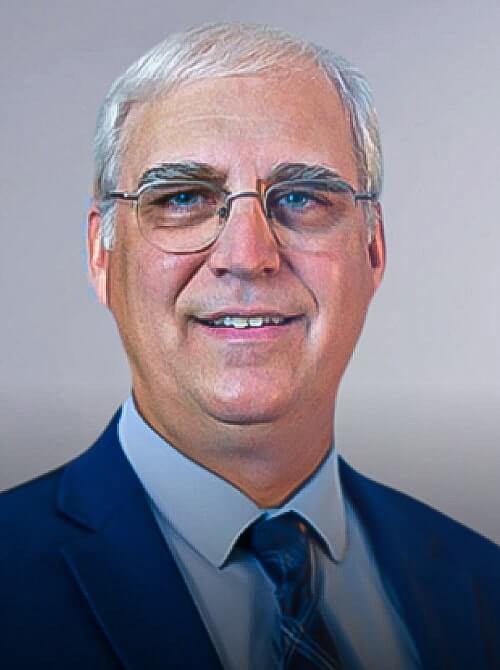
Ray Sheen
Project Management Instructor & Author
Accreditations
Link to awards GoSkills Ltd is an IASSC Accredited Training Organization™. The PMI ATP seal, PMI, PMP, CAPM and PMBOK are registered marks of the Project Management Institute, Inc.How GoSkills helped Chris
I got the promotion largely because of the skills I could develop, thanks to the GoSkills courses I took. I set aside at least 30 minutes daily to invest in myself and my professional growth. Seeing how much this has helped me become a more efficient employee is a big motivation.
