Lean Six Sigma Basics: Intro to Lean Six Sigma
Intro to Lean Six Sigma
Skills you’ll gain
Kick off your Lean Six Sigma education with this tutorial on Lean Six Sigma basics.
Lean Six Sigma is today’s pre-eminent quality improvement methodology. But it hasn’t always been that way. In this tutorial, Ray Sheen will take you through the history of Lean and Six Sigma, and will show you some of the Lean Six Sigma fundamentals that will be important to your success in process improvement.
This introduction to Lean Six Sigma offers a starting point for you to start building foundational knowledge about this continuous improvement framework. By the end of this tutorial you will be ready to dive deeper into the Lean Six Sigma curriculum and start working towards your Lean Six Sigma certifications.
This tutorial includes:
- Six easy to digest Lean Six Sigma lesson videos
- Downloadable exercise files and reference guides
- Unlimited quiz and test attempts
- Certificate of completion
Over the course of six lessons, you will learn:
- The history and evolution of quality improvement programs
- The guiding principles of both Six Sigma and Lean manufacturing
- How Lean and Six Sigma are combined to complement each other
- The five phases of a Lean Six Sigma project
- What occurs in each project phase and the deliverables that are created
Want to learn more? We offer Lean Six Sigma courses in three tiers to suit your needs. Try taking our Yellow Belt course, Green Belt course series, and Black Belt course series.
Syllabus
Download syllabusCertificate
Certificate of Completion
Awarded upon successful completion of the course.

Instructor
Ray Sheen
Ray is a certified Project Management Professional (PMP) with the Project Management Institute, a certified Scrum Master with Scrum Alliance, and certified Lean Six Sigma Black Belt with IASSC. He is a member of the Project Management Institute and the Product Development Management Association.
He is president and founder of Product & Process Innovation, Inc. and is a veteran business leader with over 25 years of executive, project management, and engineering management experience. Ray has worked in several industries including aerospace, electrical distribution and utilities, biotechnology, appliances, electronics, machining, medical devices, pharmaceutical, automotive, and financial services. He has held executive management positions in a Fortune 500 company and has been involved in entrepreneurial startup organizations.
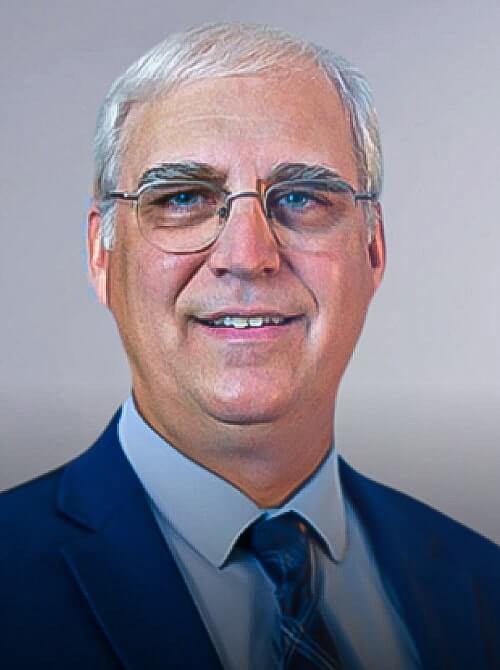
Ray Sheen
Project Management Instructor & Author
Accreditations
Link to awardsHow GoSkills helped Chris
I got the promotion largely because of the skills I could develop, thanks to the GoSkills courses I took. I set aside at least 30 minutes daily to invest in myself and my professional growth. Seeing how much this has helped me become a more efficient employee is a big motivation.
