Lean Six Sigma Advanced Principles - Black Belt
Lean Six Sigma Advanced Principles - Black Belt
Skills you’ll gain
This course is part of our Lean Six Sigma Black Belt program, which consists of eight courses designed to prepare you for the International Association of Six Sigma Certification (IASSC) Black Belt exam. We recommend you take all eight courses in the program to be fully prepared for the exam.
In high demand across a diverse range of industries, Lean Six Sigma training is a powerful way to become an indispensable asset at your organization and improve your career prospects.
Lean Six Sigma Black Belts are subject matter experts who guide and mentor junior members of the organization while driving improved performance and efficiency throughout the company.
In this online course, you will master the advanced Lean Six Sigma principles, tools, and methodology required to lead a Lean Six Sigma project as a Black Belt practitioner. In addition to the leadership skills and knowledge you will acquire, pursuing Lean Six Sigma certification can put you on the fast track for lucrative executive and management roles, and boost your salary.
Course highlights:
- Aligned to the IASSC Lean Six Sigma Black Belt Body of Knowledge.
- Expert instruction by a certified Project Management Professional (PMP) with the Project Management Institute, Scrum Master with Scrum Alliance, and Lean Six Sigma Black Belt with IASSC. Ray Sheen is a member of the Project Management Institute and the Product Development Management Association.
- 87 practical tutorials with videos, reference guides, exercises, and quizzes.
- Earn 30 PDUs or contact hours toward your Project Management education for certification with PMI.
In this course, you will:
- Understand the requirements and application process for Lean Six Sigma certification with internationally recognized accreditation body, IASSC.
- Learn the roles, phases, and deliverables of a Lean Six Sigma project and your responsibilities as a Black Belt project leader.
- Master Lean Six Sigma fundamentals, including Critical to Quality (CTQ), variation, and process management.
- Become a subject matter expert in the five phases of DMAIC: Define, Measure, Analyze, Improve, and Control.
- Learn techniques to coach stakeholders and provide positive and negative feedback.
- Identify the deliverables required for each Stage gate review and how to isolate issues.
- Review the latest Lean Six Sigma certification syllabus updates, including: Multi-variate analysis, Pugh concept generation, Design for Six Sigma, and more.
The only method to earn an IASSC certification is to successfully sit for and pass an official IASSC certification™ exam, which can be taken through IASSC. We do not provide access to IASSC Certification exams.
Looking for something else? We offer a range of project management and Lean Six Sigma online training, including Yellow Belt and Green Belt certification courses.
Once enrolled, our friendly support team and tutors are here to help with any course-related inquiries.
Syllabus
Download syllabus-
1
IASSC Testing Approach The International Association of Six Sigma Certification is a recognized international body that certifies Lean Six Sigma Yellow, Green, and Black Belts. The online application process is straightforward. 5m
-
2
IASSC Black Belt This lesson provides a high-level review of the topics covered on the IASSC Black Belt examination. 7m
-
1
Roles and Responsibilities The Lean Six Sigma methodology has defined roles of Yellow Belt, Green Belt, Black Belt, and Master Black Belt with respect to project leadership and execution. In addition, there are roles and responsibilities for team sponsors, team members, and others who become involved with a Lean Six Sigma project. 4m
-
2
Project Phases The Lean Six Sigma methodology relies on a five-phased project management methodology. The phases Define, Measure, Analyze, Improve, and Control provide structure to the project. 5m
-
3
Project Deliverables The Lean Six Sigma methodology has defined a set of deliverables that should be prepared during each of the five project phases. These deliverables will guide a project team through the improvement process in an orderly and logical manner. 5m
-
4
Project Charter A best practice for any project is to create a project charter at the time of project initiation. The Lean Six Sigma project charter will focus on the scope of the project, the timing for the project milestones, and the key team members. This provides a basis for project planning. 4m
-
5
Business Case Businesses require a rationale before allocating resources to a project. This principle applies to Lean Six Sigma projects. The business case explains the business impact of the defect or problem situation the project will be attempting to resolve. In most cases, this defect or problem must be translated into a fiscal impact in order to prioritize the problem with respect to other problems that could also have a Lean Six Sigma project assigned. 5m
-
6
Project Reviews The Lean Six Sigma methodology involves stakeholders through a set of project reviews. Each type of review has a goal and purpose. 5m
-
7
Coaching Stakeholders The Lean Six Sigma Black Belt is often the primary interface between Lean Six Sigma teams and senior management stakeholders. Many of these stakeholders do not understand the Lean Six Sigma methodology. The Lean Six Sigma Black Belt will need to manage the stakeholder interactions and coach the stakeholders concerning their role in a Lean Six Sigma project. This lesson will discuss the roles of stakeholders and stakeholder interactions. 6m
-
8
Coaching with Questions A Lean Six Sigma Black Belt will often need to coach Green Belts, Yellow Belts, and other team members. Through the effective use of questions, the Black Belt can both gain information for themselves and provide training in quality thinking and the improvement methodology. Different questioning techniques are appropriate for different team circumstances. This lesson will review the techniques and when to apply them. 5m
-
9
Coaching with Feedback Feedback, both positive and negative, can be a very effective tool for Lean Six Sigma Black Belts to use when coaching teams. However, feedback used inappropriately can damage the team and undermine their ability to achieve a project success. This lesson will discuss the use of feedback and provide pointers for how to deliver it. 6m
-
1
Critical To Quality (CTQ) Lean Six Sigma relies on the use of Critical to Quality (CTQ) characteristics. These are the attributes that will be used to measure success or failure of the project. 4m
-
2
Writing CTQs A well-written Critical to Quality (CTQ) characteristic becomes a goal for aligning the Lean Six Sigma project activities. A poorly written CTQ leads to confusion in the analysis and uncertainty with respect to the project's success or failure. There is a recommended template and format for writing CTQs. 5m
-
3
Variation Variation leads to uncertainty in process performance which requires extra management and buffers elsewhere in the business environment. One of the primary goals of a Lean Six Sigma project is to identify sources of variation in process performance and eliminating or reducing those sources of variation. 6m
-
4
Elements of Waste Waste can take many forms including high costs, delayed timing, rework, redundant work and idle processes. One of the primary goals of a Lean Six Sigma project is to identify areas of process waste and eliminating or reducing those sources of waste. 6m
-
5
Y=F(x) Lean Six Sigma projects strive to characterize project performance through the creation of a process formula. This formula allows the team to determine controllable factors and predict and optimize process performance. 4m
-
6
Process Management Lean Six Sigma analysis considers process level performance. For this reason it is necessary to understand the complete process – both the process steps and the process flow. 5m
-
7
Project Metrics Lean Six Sigma has introduced some new metrics into the common business vocabulary including process sigma, DPMO, cycle time, and value-added effort. 8m
-
1
Project Selection One of the decisions that must be made during the Define Phase is the selection of the project and its boundaries. Lean Six Sigma projects are often part of a portfolio of projects that may be selected and approved as a bundle. 5m
-
2
Pareto Principle The Pareto principle is a widely accepted technique for prioritizing effort and activity. The Pareto principle will typically be applied in every phase of a Lean Six Sigma project, including this initial Define phase where it is used to prioritize the areas of focus for the project. 4m
-
3
Voice of the Customer Lean Six Sigma methodology is grounded on the voice of the customer. The Define phase collects and assesses information concerning the customer perspective and uses it to focus the project activities. 6m
-
4
Cost of Poor Quality (COPQ) Lean Six Sigma is a problem-solving methodology. As such, one of the ways of quantifying the opportunity for improvement is through an aggregation of the costs associated with that problem. This is known as the Cost of Poor Quality and provides insight into the project benefit. 7m
-
5
Process Mapping In order to improve process performance, the Lean Six Sigma project team must understand the current state of the process. Process Mapping is the technique for describing the process and providing a framework for collecting process data. 5m
-
6
Lean Value Lean Six Sigma projects apply the Lean principle of value-added effort in the definition of the project and when identifying the opportunity for improvement. 5m
-
7
Define Stage Deliverables A Lean Six Sigma Black Belt will often chair the Stage Gate Review meetings for Lean Six Sigma Projects. In those meetings, the Black Belt needs to ensure the work of the phase was done and the tools were used effectively. This lesson reviews the normal deliverables due at the Define Stage Gate review. It also includes hints and tips for identifying problems to be avoided during that phase. 6m
-
1
Problem Statement The problem statement clarifies the goals and activities of the Lean Six Sigma project by specifying the issue to be resolved. It's an excellent communication tool for the team to use with stakeholders. 4m
-
2
Problem Definition Tools There are numerous tools to assist the Lean Six Sigma team in the creation of the problem statement. Different tools work better in different applications, but all of them help the Lean Six Sigma team focus on the root cause problems and not chase symptoms. 6m
-
3
Data Types There are three types of data: variable, attribute and ranked. Each type is useful in measuring process performance by analyzing process problems, but they need to be treated differently. 5m
-
4
Measurement Systems The collection of data assumes that there is a measurement system used to measure and record the data. It is important to understand the characteristics of the measurement systems so that the Lean Six Sigma team will know how far they can trust the data. 5m
-
5
Measurement Errors All measurement systems introduce an element of error into the measured value. There are techniques for determining the magnitude of that error and thereby determining if a different measurement system needs to be used. 5m
-
6
X/Y Matrix The X/Y Matrix is a tool that maps the Voice of Customer needs and concerns (Y) onto the process steps and inputs (X). This tool can take on several different formats, but any of them will provide the Lean Six Sigma team with insight into the contributing factors of customer value. 4m
-
7
Intro to FMEA The Failure Mode Effects Analysis (FMEA) tool highlights areas of high product design or process execution risk. This tool provides insight into possible causes for observed failures. 6m
-
8
Value Stream Mapping Value stream mapping is the Lean process mapping technique. With this map, the Lean Six Sigma team will know which steps are directly contributing to delivering the customer value aspects of the process. It also provides the foundation for deeper flow analysis. 4m
-
9
Value Stream Map Data Box The Value Stream Map Data Box is the technique used to capture and analyze data at each step of the Value Stream Map. 6m
-
10
Value-Added/Non-Value-Added A portion of each step in a Value Stream Map is allocated to the value-added effort, which is work done that creates customer value. All other time and effort in the step is non-value added. In many cases, the entire step is non-value added. 6m
-
11
As-Is Metrics The As-Is metrics are the measured current state of the process or problem. It is not the best case, the worst case, or the “as-designed” case; it is the current average performance of the process or problem. 5m
-
12
Data Collection The purpose of the Measure phase of a Lean Six Sigma project is to collect complete, accurate, and meaningful data. There is a simple data collection approach that can be used by the team to ensure this is accomplished. 7m
-
13
Measure Stage Deliverables A Lean Six Sigma Black Belt will often chair the stage gate review meetings for Lean Six Sigma projects. In those meetings, the Black Belt needs to ensure the work of the phase was done and the tools were used effectively. This lesson reviews the normal deliverables due at the Measure stage gate review. It also includes hints and tips for identifying problems to be avoided during that phase. 6m
-
1
Descriptive Statistics Lean Six Sigma methodology relies heavily on statistical analysis of problems and solutions. A single data point is not sufficient, rather a collection of data is needed for analysis. This collection will have some natural variability within it and descriptive statistics explain the boundaries of that variability. 6m
-
2
Sample versus Population Statistics When doing Lean Six Sigma statistical analysis, you are often working with a small sample of the potential data associated with the problem. We analyze the sample data and from that we can make inferences about the full data population for the problem. 4m
-
3
Normal Distribution The normal distribution charts the type of variability in a process parameter that is being measured when the only cause for variation is natural random physical effects. It's the desired distribution when improving a process since it delivers a predictable level of process performance. 6m
-
4
Basic Graphical Analysis When considering a distribution of data values for a process attribute, a graph of that data can be very insightful. The picture is often easier for team members to understand than a statistical description of the data distribution. This picture will often point the team to the process problem. 4m
-
5
Graphing of Complex Data When the process or problem data set has multiple characteristics, there are a set of graphing techniques that can show these effects. Although more complex than the basic techniques, they are easy to use and create a picture of the data set. 8m
-
6
Process Stability A stable process is one in which only random variation exists. A Lean Six Sigma team must eliminate sources of instability before attempting to improve the normal process performance. The key is undertanding common cause and special cause variation.. 6m
-
7
Run Chart The run chart is the most common chart of process data. It is easy to create and maintain and gives the process operators immediate insight when a process becomes unstable. 5m
-
8
Z Transformation The Z transformation is a technique that converts a data value into the number of standard deviations it is above or below the mean of the distribution. This provides an opportunity to compare between data sets and to estimate process yield rates. 5m
-
9
Process Capability - Variable Data Process capability is the statistical analysis conducted to determine if a process performing with only the normal process variation can be expected to meet the customer's expectations at all times. Variable data process capability is tracked with capability indices. 7m
-
10
Process Capability - Attribute Data A stable process is one in which only random variation exists. A Lean Six Sigma team must eliminate sources of instability before attempting to improve the normal process performance. To determine stability with attribute data, lookup tables and yield rates must be used. 4m
-
11
Benchmark Z and 1.5 Sigma Shift The Benchmark Z provides a second method for determining process capability. The 1.5 sigma shift accounts for long-term stability within the process variation. 4m
-
12
Central Limit Theorem The Central Limit Theorem is a principle that is used to transform non-normal raw data into a data set that is normal. 4m
-
1
Problem Analysis Problem analysis is the methodical approach to analyzing a problem and finding the root cause or causes. It normally includes creating and testing an hypothesis or an experiment to determine the cause. 5m
-
2
Basic Visual Analysis Visual analysis techniques are particularly good for illustrating significance, similarities or differences, and correlation between parameters within a data set. Visual data may provide insights that are hidden in statistical analysis 5m
-
3
Advanced Visual Analysis Various graphical analysis techniques can help illustrate comparisons, relationships, distributions, or compositions. Selecting the correct graphical technique can illustrate what is significant, and the wrong technique can lead to confusion. 5m
-
4
Statistical Analysis Statistical tests are often used to aid the problem analysis. The result of the test is a statistical measure of the validity of a hypothesis about the problem in the sample with an inference about that problem throughout the data population. 5m
-
5
Advanced Statistical Analysis The statistical analysis of a small sample of data can point to root causes of problems in the full data set. The selection of the correct statistical test is key to conducting an effective analysis. 4m
-
6
Lean Flow Analysis The Lean process analysis will reveal flow process problems. Lean techniques can be used to analyze flow at a total process (macro) level or a process step (micro) level. 6m
-
7
Lean Quality Analysis The process analysis of the value stream map will reveal quality issues that are occurring within process steps. These are identified by analyzing step data and process flow data. 5m
-
8
Lean Resource Analysis Analysis of the Lean value stream map and the related data can reveal wasted resources; both people and product or service items that are being processed. 5m
-
9
Analyze Stage Deliverables A Lean Six Sigma Black Belt will often chair the stage gate review meetings for Lean Six Sigma projects. In those meetings, the Black Belt needs to ensure the work of the phase was done and the tools were used effectively. This lesson reviews the normal deliverables due at the Analyze stage gate review. It also includes hints and tips for identifying problems to be avoided during that phase. 5m
-
1
Problem Improvement Problem-solving often requires an interim solution while a permanent solution is being developed and validated. When multiple possible solutions are available, the team should recommend a solution approach. 7m
-
2
Pugh Concept Generation The Pugh Concept Generation technique is an ideation technique that is often used to facilitate brainstorming sessions focused on finding a solution for a problem. The technique compares various concepts to identify ones with the most promise and benefit. 5m
-
3
Solving Special Cause & Common Cause Problems Special cause problems should be resolved first in order to achieve process stability. Then common cause problems are addressed to reduce process variation. 5m
-
4
Intro to Design of Experiments Design of Experiments (DOE) is an experimental technique for identifying the primary factors within a system that determine system performance. DOE is particularly useful in complex systems where there are interactions between factors and relationships are not obvious. 5m
-
5
Lean Improvement: Flow Lean process improvements are designed based on problems found in the value stream map that show the new flow. The flow improvements are concerned with overall process design and constraints along with the design of individual steps. 6m
-
6
Lean Improvement: Pull The benefits of Lean improvements rely on changing the process schedule management approach in addition to process redesign. Pull scheduling and visual management are used to maintain smooth flow in the process. 6m
-
7
Solving Problems with Poka Yoke Many problems can be solved using mistake proofing approaches that are embodied in the five Poka Yoke principles that both detect and prevent errors from occurring. 5m
-
8
Solving Problems with Five S Disciplines The Five S disciplines can be used to organize the workplace and support and sustain the problem solutions by reducing the likelihood of confusion and rapidly exposing process degradation. 5m
-
9
To-Be Value Stream The To-Be process map or value stream map is the proposed new process that has incorporated the flow improvements, five “S” changes, and Poka Yoke aspects at each step. This map is the plan for process change. 5m
-
10
Innovation and Concept Selection When the improvement required needs to be more than an incremental change to the existing product or process an ideation technique is needed. Once ideas for problem solutions are identified, the best option must be selected. 5m
-
11
Intro to Design for Six Sigma Design for Six Sigma is a new product development methodology. It focuses on meeting external and internal needs so that the product is immediately successful at product launch. 5m
-
12
Improve Stage Deliverables A Lean Six Sigma Black Belt will often chair the stage gate review meetings for Lean Six Sigma projects. In those meetings, the Black Belt needs to ensure the work of the phase was done and the tools were used effectively. This lesson reviews the normal deliverables due at the Improve stage gate review. It also includes hints and tips for identifying problems to be avoided during that phase. 6m
-
1
Cost-Benefit Analysis The cost-benefit analysis quantifies the financial impact of the Lean Six Sigma project. It includes the project costs and the operational impacts which could include cost savings, new cost of new operations, and the gross margin impact of additional sales. 3m
-
2
Calculating Business Benefit The proof of the benefit of a Lean Six Sigma team’s solution will be found in the measured change in the process performance. The calculation quantifies this impact. 6m
-
3
Control Plan It is hard to make a permanent change to a process. People and systems have a tendency to drift back to the old way of doing things. The control plan provides guidance on how to maintain control of the new process and the measurements that will show the process deviating from the new approach. 4m
-
4
Response Plan A key element of the control plan is the response plan. It tells the process operators what to do when the process begins to deviate from the parameters laid out in the control plan. 7m
-
5
Prevention as Control One of the best techniques for controlling a process to perform in a particular manner is to prevent it from performing in any other manner. There are methodologies that can be used to create prevention of process problems: Poke Yoke and Five S Disciplines. 6m
-
6
Lean Process Control Lean process control focuses on maintaining the process flow of the Should-Be process. It relies on principles of visual control, empowerment, and continuous improvement. 6m
-
7
Statistical Process Control Statistical process control uses real-time process data to determine whether a process is maintaining the improvements that were implemented. Control charts will indicate special cause and common cause variation, empowering process operators to maintain process quality. 5m
-
8
Implementing the Solution Implementing the technical changes of the solution is often easy; the difficulty is usually the emotional and cultural resistance to change. The implementation should be planned and managed as a project. The project should include the actions taken to change the business systems and structures in addition to the specific problem solution. 6m
-
9
Control Stage Deliverables A Lean Six Sigma Black Belt will often chair the stage gate review meetings for Lean Six Sigma projects. In those meetings, the Black Belt needs to ensure the work of the phase was done and the tools were used effectively. This lesson reviews the normal deliverables due at the Control stage gate review. It also includes hints and tips for identifying problems to be avoided during that phase. 6m
Certificate
Certificate of Completion
Awarded upon successful completion of the course.

Instructor
Ray Sheen
Ray is a certified Project Management Professional (PMP) with the Project Management Institute, a certified Scrum Master with Scrum Alliance, and certified Lean Six Sigma Black Belt with IASSC. He is a member of the Project Management Institute and the Product Development Management Association.
He is president and founder of Product & Process Innovation, Inc. and is a veteran business leader with over 25 years of executive, project management, and engineering management experience. Ray has worked in several industries including aerospace, electrical distribution and utilities, biotechnology, appliances, electronics, machining, medical devices, pharmaceutical, automotive, and financial services. He has held executive management positions in a Fortune 500 company and has been involved in entrepreneurial startup organizations.
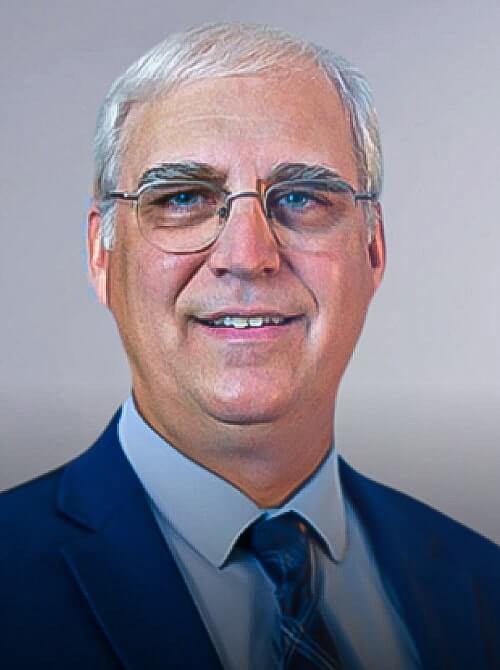
Ray Sheen
Project Management Instructor & Author
Accreditations
Link to awards The PMI ATP seal, PMI, PMP, CAPM and PMBOK are registered marks of the Project Management Institute, Inc.How GoSkills helped Chris
I got the promotion largely because of the skills I could develop, thanks to the GoSkills courses I took. I set aside at least 30 minutes daily to invest in myself and my professional growth. Seeing how much this has helped me become a more efficient employee is a big motivation.
