Statistical Process Control Training Course Online - GoSkills.com
Statistical Process Control
Skills you’ll gain
This course is part of our Lean Six Sigma Green Belt program, which consists of four courses designed to prepare you for the International Association of Six Sigma Certification (IASSC) Green Belt exam. We recommend you take all four courses in the program to be fully prepared for the exam.
Statistical process control allows you to visually see and understand what is happening with a process in real time. SPC techniques help you manage and control processes with data, and warn you when the process has degraded and action is needed.
In this course you will learn how to create and use control charts, the heart of statistic process control, to improve your business processes.
The training features plenty of opportunities to practice with examples, exercises and quizzes to test your knowledge. By the end of the course, you will have the skills to conduct simple, straightforward analysis to improve processes at your company.
The course is designed from the standpoint of making sound business decisions for improving processes. You won’t need to do any advanced math or derive proofs behind the formulas or statistics. Instead, you’ll learn how to use popular programs like Excel and Minitab to do the calculations for you. While the computer crunches the numbers, you will learn how to read the data and analyze the results of the study.
Highlights:
- 26 practical tutorials with videos, reference guides, exercises and quizzes.
- Designed to prepare you in part for the IASSC Green Belt exam. To prepare in full, you should also take the Lean Six Sigma Principles, Measurement Systems Analysis, and Hypothesis Testing courses part of our four course Lean Six Sigma Green Belt program.
- Understand statistical control principles such as variation and non-normal variation.
- Learn how to create control charts in Excel with the Data Analysis add-in.
- Learn how to use Minitab to calculate descriptive statistics for a data set.
- Identify the difference between special cause variation and common cause variation.
- Understand the principle of process capability and how to calculate it for variable and attribute data.
- Learn the strategy behind using control charts, and their limits.
- Create different kinds of control charts, including X Bar-R, X Bar-S, Variable Data, Attribute Data, and more.
- Aligned to the IASSC Lean Six Sigma Green Belt Body of Knowledge.
- The only method to earn an IASSC certification is to successfully sit for and pass an official IASSC certification™ exam, which can be taken through IASSC. We do not provide access to IASSC Certification exams.
- Earn 4 PDUs or contact hours toward your Project Management education for certification with PMI.
Once enrolled, our friendly support team and tutors are here to help with any course related inquiries.
Syllabus
Download syllabus-
1
Common Cause - Special Cause SPC Control Charts are designed to differentiate between special cause variation and common cause variation. In order to understand the importance of this and the implication for control, this lesson explains and illustrates the differences. 6m
-
2
Process Capability Process Capability consists of comparing the Voice of the Customer to the Voice of the Process. SPC Control Charts provide a quantitative measure of the Voice of the Process. This lesson explains the principle of process capability and the role of SPC in achieving and maintaining it. 6m
-
3
Process Capability with Variable Data Process Capability is often correlated with process Sigma. The calculation of process capability is quite different depending upon whether the data is variable or attribute data. This lesson will present the technique and practice using the variable data process capability ratios. 6m
-
4
Process Capability with Attribute Data Six Sigma projects strive to achieve a process capability that represents Six Sigma quality. The calculation of process capability is quite different depending upon whether the data is variable or attribute. This lesson will present the technique used for determining process capability with attribute data. 6m
-
1
Control Chart Design This lesson explains how a control chart works. The various elements of a control chart are described and the correlation between the data shown on Control Charts and process stability is discussed. 4m
-
2
Statistical Control Strategies In this lesson the strategy for how to use Control Charts is discussed. In addition to monitoring the process, the charts can be used to set performance baselines, validate the impact of improvement, and identify sources of variation. 6m
-
3
Control Limits This lesson explains the principles behind how control limits are calculated. The lesson also discusses when to establish limits and how to use those limits to detect special cause variation. Finally, the lesson will show how to set the threshold criteria for use with control limits in Minitab. 5m
-
4
Control Charting Process This lesson introduces the eight step approach to be used with establishing control charts for a process. In addition, it provides a decision tree for selecting which control chart to use based upon the nature of the data being monitored. 5m
-
5
SPC Corrective Actions This class reviews the appropriate and inappropriate response to be taken based upon the data found on a control chart. It reviews what steps to follow when there is special cause variation and what steps to follow with common cause variation. 7m
-
6
Subgroups and Samples Some of the most important decisions with respect to control charting are the decisions about subgroups and samples. These decisions will dictate the type of control chart that should be used. They also will determine the number of data points in a subgroup. The decisions should be made based upon the characteristics of the process that is being control charted. 6m
-
1
Variable Data Control Charts This lesson discusses the principles of using control charts with variable data and provides ground rules for data sampling. The differences between the variable data SPC control charts are explained. 5m
-
2
I-MR Chart The Individual and Moving Range chart is the simplest of the variable data control chart. This lesson explains how the data is recorded and interpreted on the chart. The lesson describes how to create this control chart in both Microsoft Excel and using Minitab. The lesson will include practice creating the chart. 6m
-
3
Xbar-R Chart The X-bar and Range chart is the most commonly used variable data control chart. When discussing SPC, this is always the example. This lesson explains how the data is recorded and interpreted on the chart. The lesson describes how to create this control chart in both Microsoft Excel and using Minitab. The lesson will include practice creating the chart. 7m
-
4
Attribute Data Control Charts This lesson discusses the unique considerations associated with monitoring attribute data with control charts. It compares and contrasts the various attribute data control charts and provides some ground rules for subgroups selection. 5m
-
5
C Chart The C chart (plots Counts) is the simplest of the attribute data control charts. This lesson explains how the data is recorded and interpreted on the chart. The lesson describes how to create this control chart in both Microsoft Excel and using Minitab. The lesson will include practice creating the chart. 4m
-
6
U Chart The U chart relies on counting both defects and units and is appropriate if the process has erratic flow. This lesson explains how the data is recorded and interpreted on the chart. The lesson describes how to create this control chart in both Microsoft Excel and using Minitab. The lesson will include practice creating the chart. 6m
-
7
NP Chart The NP Chart tracks defective units rather than actual defects. It provides a more macro perspective for the organization. This lesson explains how the data is recorded and interpreted on the chart. The lesson describes how to create this control chart in both Microsoft Excel and using Minitab. The lesson will include practice creating the chart. 4m
-
8
P Chart The P chart is closely related to the NP Chart. It also tracks units but tracks the percentage of defective units. This lesson explains how the data is recorded and interpreted on the chart. The lesson describes how to create this control chart in both Microsoft Excel and using Minitab. The lesson will include practice creating the chart. 6m
-
9
Time Weighted Control Charts This lesson introduces the concept of weighting the data being tracked in a control chart based upon other recent data values. The advantages and disadvantages of this approach are discussed as the weighting principles are introduced. 3m
-
10
CUSUM Chart The Cumulative Sum (CUSUM) Chart is more sensitive to subtle shifts in the process than the traditional variable data charts. The look of this control chart is unique among the commonly used control charts. This lesson explains how the data is calculated and interpreted on the chart. The lesson describes how to create this control chart in both Microsoft Excel and using Minitab. The lesson will include practice creating the chart. 7m
-
11
EWMA Chart The Exponentially Weighted Moving Average Chart uses both the current data point and recent data points. It is also very sensitive to small shifts in the data. This lesson explains how the data is recorded and interpreted on the chart. The lesson describes how to create this control chart in both Microsoft Excel and using Minitab. The lesson will include practice creating the chart. 5m
-
12
Xbar-S Chart The X-bar and Standard Deviation chart is the variable data control chart used when the subgroup is large. This lesson explains how the data is recorded and interpreted on the pair of control charts. The lesson describes how to create this control chart in both Microsoft Excel and using Minitab. The lesson will include practice creating the charts. 6m
Certificate
Certificate of Completion
Awarded upon successful completion of the course.

Instructor
Ray Sheen
Ray is a certified Project Management Professional (PMP) with the Project Management Institute, a certified Scrum Master with Scrum Alliance, and certified Lean Six Sigma Black Belt with IASSC. He is a member of the Project Management Institute and the Product Development Management Association.
He is president and founder of Product & Process Innovation, Inc. and is a veteran business leader with over 25 years of executive, project management, and engineering management experience. Ray has worked in several industries including aerospace, electrical distribution and utilities, biotechnology, appliances, electronics, machining, medical devices, pharmaceutical, automotive, and financial services. He has held executive management positions in a Fortune 500 company and has been involved in entrepreneurial startup organizations.
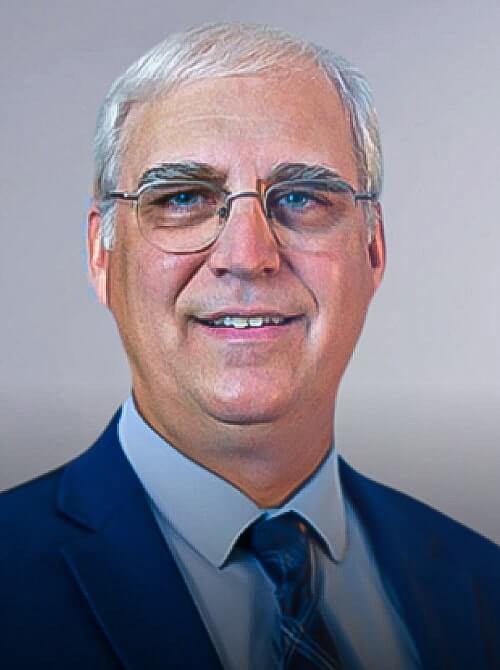
Ray Sheen
Project Management Instructor & Author
Accreditations
Link to awards GoSkills Ltd is an IASSC Accredited Training Organization™. The PMI ATP seal, PMI, PMP, CAPM and PMBOK are registered marks of the Project Management Institute, Inc.How GoSkills helped Chris
I got the promotion largely because of the skills I could develop, thanks to the GoSkills courses I took. I set aside at least 30 minutes daily to invest in myself and my professional growth. Seeing how much this has helped me become a more efficient employee is a big motivation.
